Top Menu
Our Process
Over the years since Nishiyama opened its doors, the company
has struck a balance between maintaining their original, intensely personal
hand-powered process and the selective incorporation of automation.
Their goal is to create an authentic, natural product, while allowing for
sufficient quantity to satisfy their clients. The result is a beautiful marriage
between past and present, man and machine, with quality reigning supreme.
From cocoon selection to testing, the entire process takes about
two months as every step is carefully overseen to assure perfection.
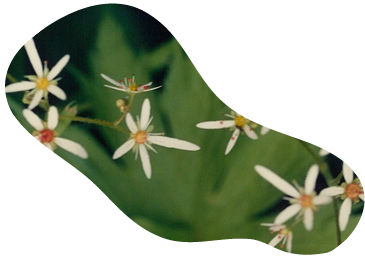
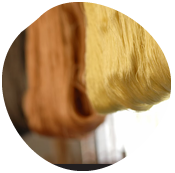
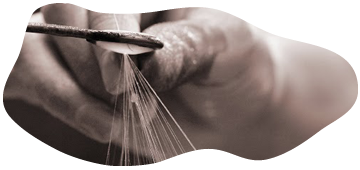
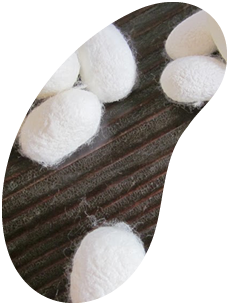
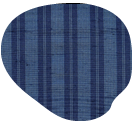
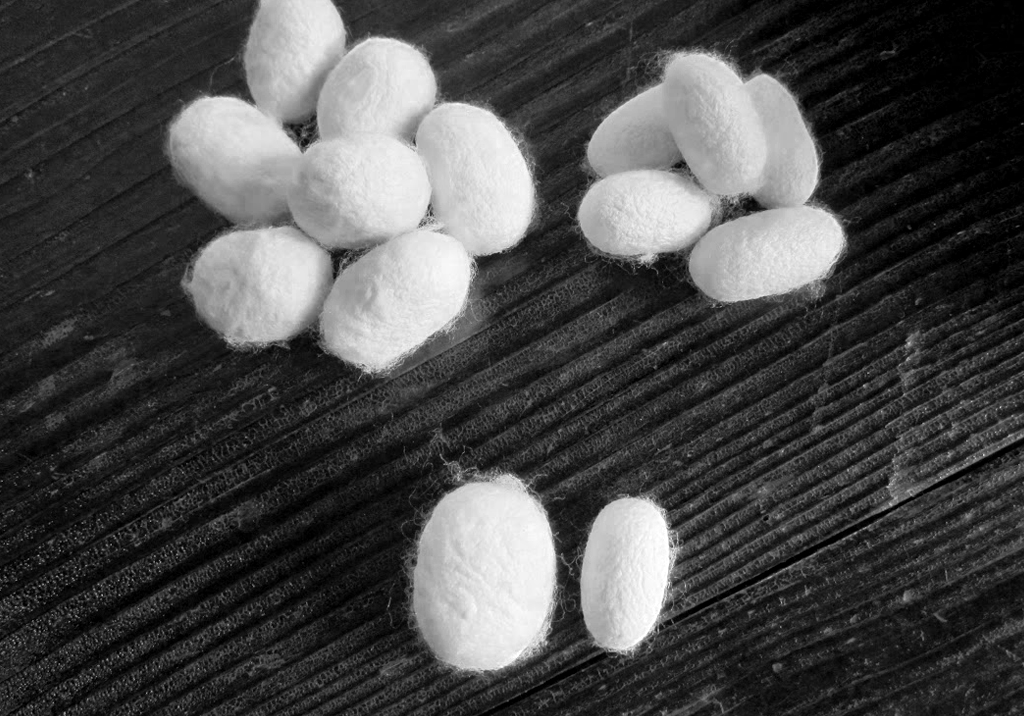
Approximately 2% of a sericulture crop
consists of doupion cocoons, single
cocoons produced by two silkworms.
Experienced workers carefully select
the best of each batch for spinning
(80 normal cocoons for the warp,
60 doupion cocoons for the woof),
with the number of cocoons used adjusted according to the thickness
of thread desired.
The cocoons are judged according
to how they feel and the condition
of the thread opening.
The cocoons are then placed in
a large iron pot and boiled to facilitate the release of the silk. They remain in the hot water until the thread is reeled,
a delicate process requiring skill and experience as there is no tool on the pedal-driven machine capable of measuring the thread’s thickness.
As the cocoons float in the pot, thread is pulled from their openings and joined to form a single strand. A treadle is engaged to reel the thread onto a small frame where it is slightly twisted.
This is an important step as
it determines the character of
the woven textile.
Threads are twisted to varying
degrees, changing the properties
of the raw silk such as strength, elasticity, consistency and coefficient of friction, and determines its thickness,luster and form.
Twisting tightly also expels air trapped inside resulting in reduced moisture and a rounder strand.
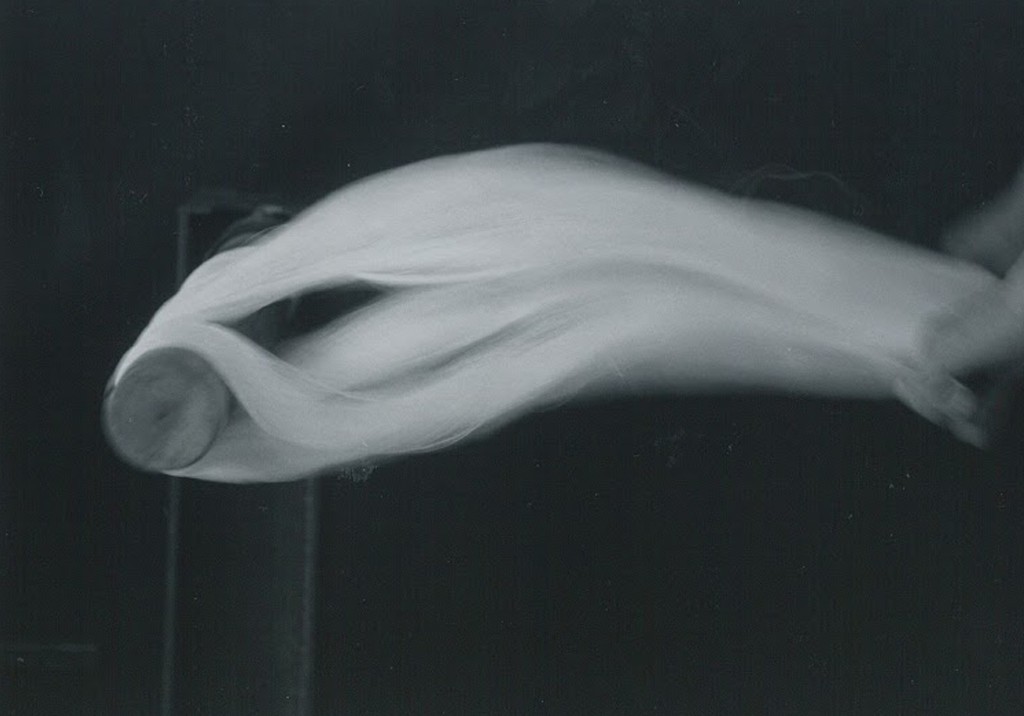
Degumming involves the removal
of the outside layer of sericin
in order to bring out the feel and
luster of the silk. Soap and sodium carbonate are dissolved in an iron
pot of boiling water.
The raw silk is put into a coarse
jute bag, boiled in the pot for about
70 minutes, and kneaded. It is then removed from the bag, carefully washed, dried and beaten. This gives
the silk thread permanent waviness. The threads are arranged to maximize airflow, making them come alive.
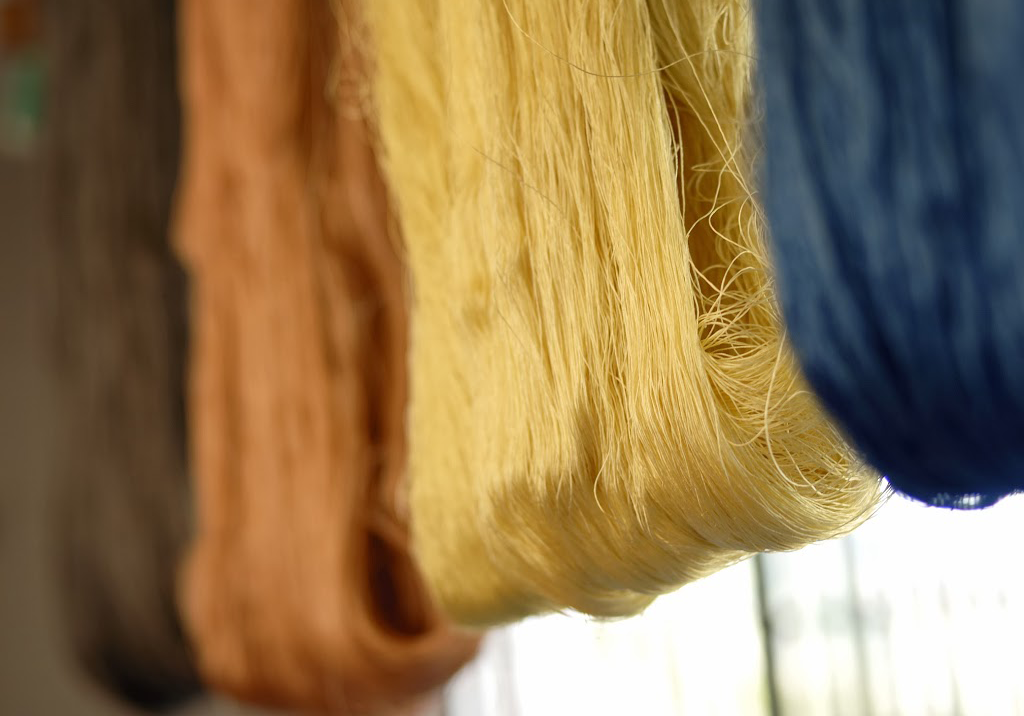
Most of the dyeing at Nishiyama is
dip dyeing using plant dyes and acid dyes. The former are made from color extracted from wild plants. The roots, bark, leaves, stems, fruit and flowers are collected when they have the highest concentration of color.
Metallic salts are combined with the extracted colors to produce a full spectrum of hues. The dyes are made in relatively small batches to maintain purity. The factory also supplements with chemical dyes in order to prolong richness and intensity of color throughout the life of the silk.
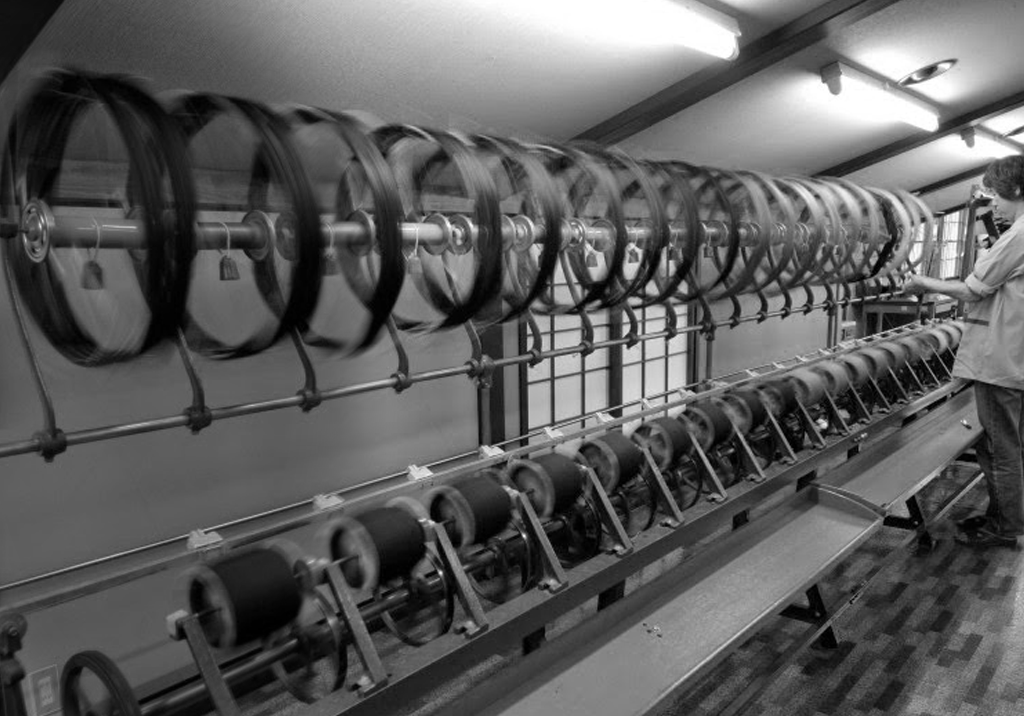
Thread which has been degummed
and dyed goes through various processes in which excessive friction and tension occur. In order to prevent the thread from becoming tangled,
and to ensure that each process goes smoothly, a kind of starch is applied
to the thread.
Nishiyama uses materials
such as funorin, wheat starch, and rice flour. Hanks of thread that have been degummed, dyed, and starched are
then spun onto a small reel with
a reeling machine.
When weaving, the woof goes through the opening made by the warp by means of a shuttle containing a spool of thread. Spooling is the process of winding the woof threads onto this spool. Small reels of thread are lined up behind the spooling machine, and the thread is wound after going through a guide above the reels.
Depending on the type of woof thread used, the tension and traverse are adjusted, and it is important to wind the thread slowly so that the spools are not pulled out of place during weaving.
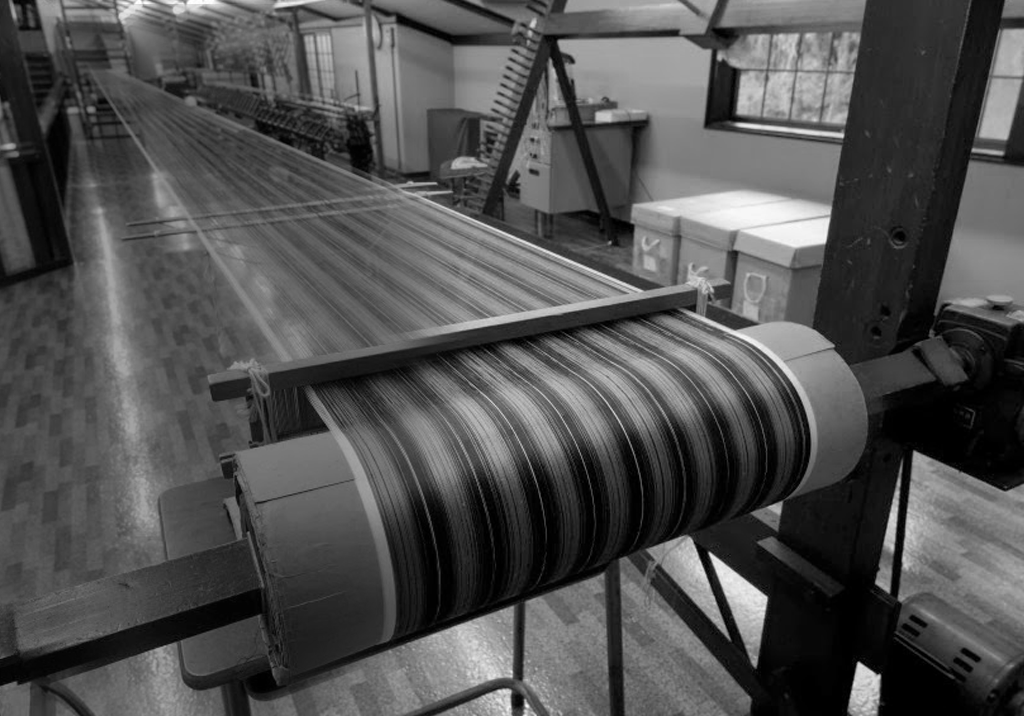
The last step in preparation
for weaving is to thread the healds
and the reed, attach the warp threads to the loom, and to make the warp threads (which have been wound onto the reel) ready for weaving.
Fifty warp threads are tied together onto the breastbeam, making sure
that there is even tension among
all the threads. The heights of the
heald and reed are adjusted so that
the threads form one line when seen
from the side.
Fabric is woven by repeatedly
opening and closing the weft threads
on the loom by the healds,
followed by the reed beating against
the breastbeam.
At Nishiyama, hand looms have been improved by equipping them with two classic shuttles of a type no longer in production but prized by designers for their rarity. The rhythm of the move-
ments has to be very accurate, and much time and practice is required to become proficient. The weaver must constantly inspect the fabric for
broken warp threads and
any other faults.
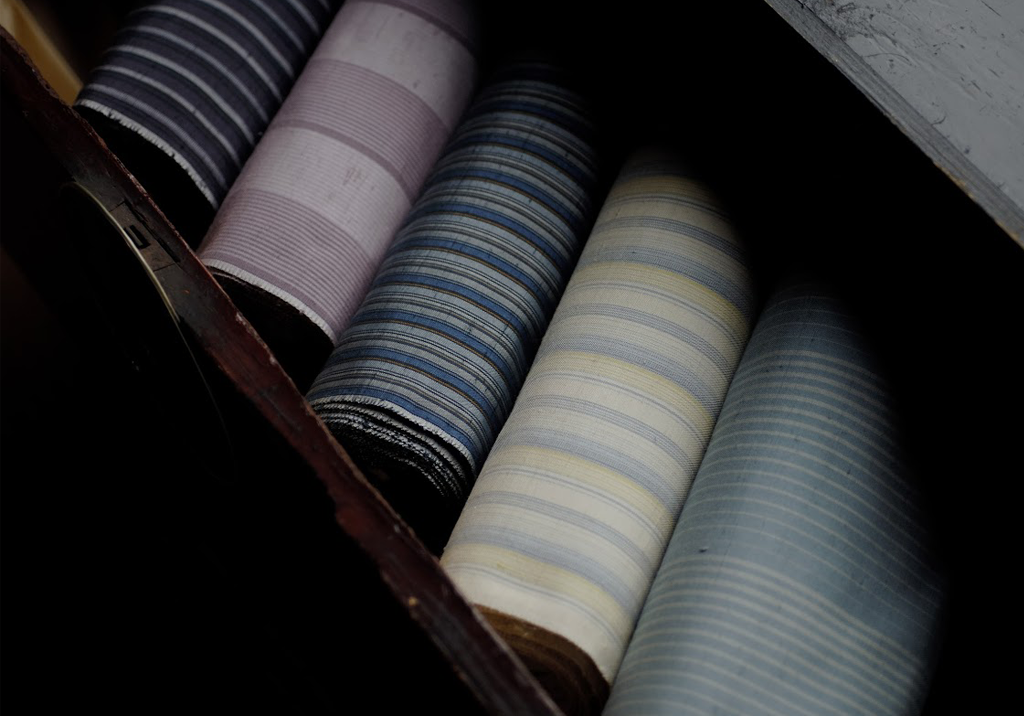
Nishiyama silk undergoes strict
testing before being put on the market, first by the association members, then by the Ishikawa Cooperative Association
for the Promotion of Ushikubi Silk, and finally an outside test is performed by the Trade and Industry Testing Office, Kanazawa Branch. The first testing takes place according to standards of width, length, weight, surface irregularity, and so on. Only textiles which conform to these stan-
dards are tested by the association. All submitted textiles are tested, but only one third of those that pass the tests are selected for outside testing.