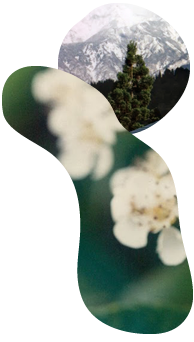
Region & History
The history of Nishiyama silk began
over 800 years ago in the remote village of Ushikubi
nestled at the foot of the Japanese Alps, near Mt. Hakusan,
one the country’s three holy mountains.
In this region, mulberry trees grow wild at high altitudes,
providing a natural environment for the silkworms to thrive,
and the clean, fresh water from the mountains
cascades through town via the Tedori River.
According to local legend, members of the Genji Clan
escaped to the village after losing the Battle of Heiji in 1159
and taught villagers the secrets of raising silkworms
and spinning and weaving silk.
Cut off from the rest of Japan for over half the year
due to extreme snowfall, silk production gave the women
an occupation and became a means of survival for the village.
Within several generations, Ushikubi had earned
a reputation for its silk, and is now designated
an Intangible Cultural Property.
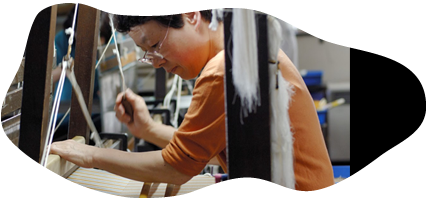
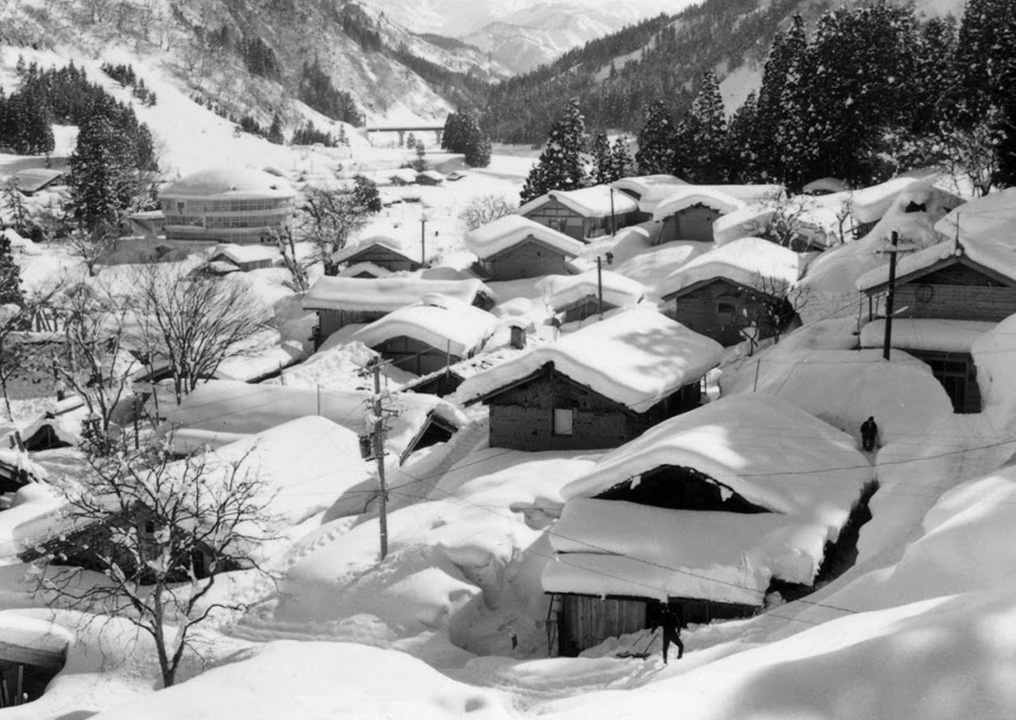
The Company
The Nishiyama family entered into silk production in the late 1950s and is now in the capable hands of the founder’s grandson, Hiroyuki Nishiyama. While the first two generations focused exclusively on the Japanese market, creating unparalleled silk for kimono and other items of traditional Japanese dress, the current president has turned his gaze outward, perceiving a much broader range of applications for his company’s unique product.
Japan is the only country still spinning silk by
hand, in addition to which Nishiyama relies on
both man-powered and automatic machines to
handle different stages in the process.
A number of these have been adapted specifically
for the European market, allowing Nishiyama to
accommodate international requests.
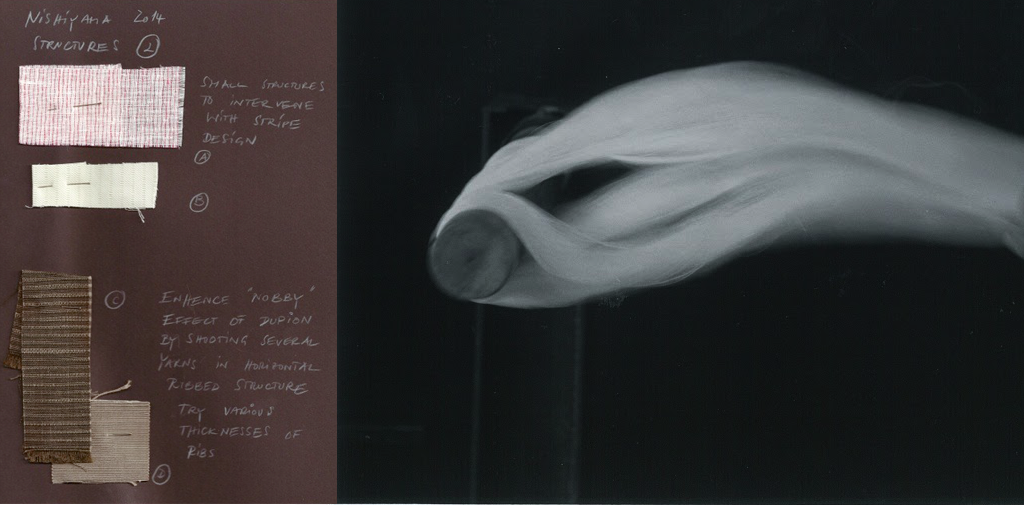
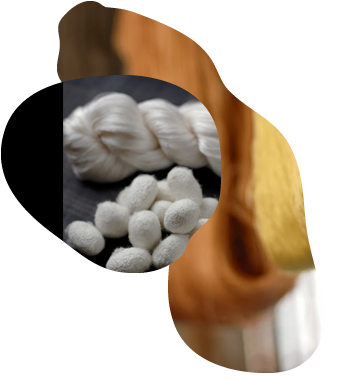
The Product
What makes Nishiyama silk so unusual
are the doupion, or “double cocoons” inhabited by two silkworms.
The thread produced by these cohabitants has many features:
elasticity, lightness, warmth-retention, and moisture absorbency,
though perhaps its most cherished trait is the variation of
strand widths that give the finished cloth its distinctive texture,
as well as considerable strength.
Locals say that if the silk catches on a nail,
it’s strong enough to pull the nail out, earning it the
nickname kugi nuki tsumugi or ‘nail-pulling silk.’
20 to 30 cocoons are required to produce one skein of silk,
and over 4000 cocoons are used to make a single kimono.
Nishiyama uses predominantly natural dyes for its silk,
including several hues made from the black lilies that grow
only in the Hakusan region. Many locals believe that the colors
of the silk dyed by this particular lily reveal the spirits of Mt. Hakusan.
Others say that every yard of Nishiyama silk embodies
the hearts and souls of the local men and women responsible
for its creation, so that any garment or fabric realized from this
special silk carries with it the power of human kindness.
Nishiyama uses the nanotechnology water
repellent finish AmberGuard to further protect its silk.
A completely organic product, AmberGuard combines
pine resin with a soluble water repellent to produce an
eco-friendly material that creates a water-shedding effect,
protecting the silk and reducing wrinkles.
If the silk catches on a nail,
it is strong enough to pull
the nail out.
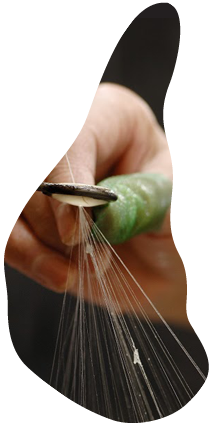
Our Clients
One of Nishiyama’s trademark patterns is the stripe,
a staple in their collection since the beginning. The stripe
gained popularity in Japan during the Edo period (1603-1867),
worn in silk by the aristocracy and in cotton by everyone else.
Over the years, this simple pattern came to represent
refined taste and an awareness of current trends. Fast forward
to the Showa period (1926-89) and the emergence
of Nishiyama Silk, where this classic staple has been
given new life and a fresh energy.
Where Nishiyama Silk once served the local community,
today this unparalleled product appeals to merchants
and designers from around Japan and beyond.
The haute couture houses of Paris and Milan have also begun
to take notice of Nishiyama, resulting in elegant and original
contemporary fashions as well as stylish accessories.
The marriage of quality, tradition and contemporary
design leaves endless possibilities.
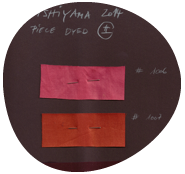
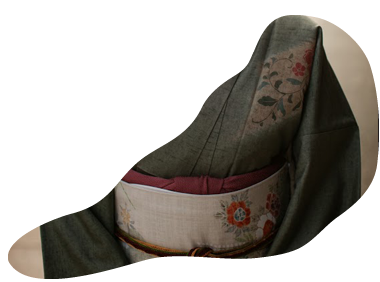
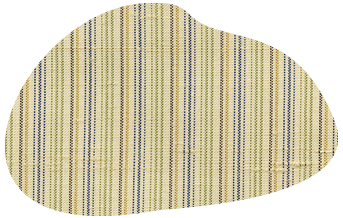